"vitri" - meaning glass
A revolutionary new manufactured glass bead containing 99.5% mixed waste glass which results in tiny spheres with outstanding properties.

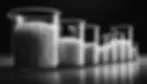

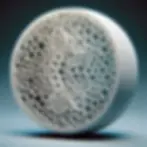
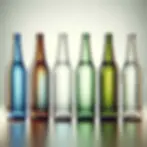


Made From 100% Recycled Waste Glass
Outer Glass Shell
-
Spherical uniformity improves crush strength
-
Uniform spherical shape aids in handling and filling / compounding
-
Smooth surface area allows for maximum chemical coupling
Honeycomb Internal Cell Structure
-
Hollow cells reduce weight
-
Air gaps provide natural insulative properties
-
Structure supports and improves outer shell crush strength
* Patent Pending
Overall Properties
-
Use of 100% Post-Consumer Recycled curbside glass
-
Complete manufacturing control of size and density
-
Beads precoated with sizing agent for the application
-
Inert nature of glass provides high temperature tolerance
INNOVATION
Why Revitri Glass Bead Is Unique
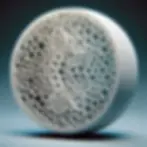
BENEFITS
Breakthrough Characteristics
01
Strength
Our bead has a strong outer glass shell with a cellular hollow inner core supporting the outer shell. Superior uniaxial crush strength is derived from the spherical shape, the glass shell, and the inner supporting structure.
02
Weight
The cellular structure with hollow gaps reduces overall weight while contributing to its superior crush strength. Lightweight beads are perfect for reducing an overall product weight with out sacrifice of strength.
03
Thermal Resistance
The hollow cellular structure provides resistance to temperature differentials and insulates along with the other characteristics. This same resistance contributes to sound dampening as well.
04
Flowability
The spherical form of the bead makes it easy to feed and flow when when combined in the substrate. Ideal for consistent distribution and when extruding.
05
Waste Glass
The bead is manufactured with 99.5% recycled, mixed colored waste glass which is found in overabundance at the glass recyclers. The over supply of this mix ends up in the landfill.
06
Size Range
The bead can be made to target diameter range, as small as 50 micron and as large as 20 millimeters while maintaining the above characteristics. Size is very dependent on the application. Variation of sizes with in a range allow for a tightly packed orientation maximizing the characteristics.
07
Density Range
The bead can be made to a target density. Higher density beads contribute to the overall strength. Lower density beads are still strong but the strength contribution is lower. A density range can be achieved from 0.2 g/cc to 2.0 g/cc with the formulation.
POTENTIAL
Applications
Plastics
Thermoplastic resin compounds for injection molded parts. Markets include automotive, aerospace, and marine.
3D Print
Our bead used as an additive for 3D print & extrusion can yield higher performance and provide insulation for 3D printed building structures.
Concrete
Using large beads as an aggregate has proven to provide exceptional crush strength without adding weight and increasing R-value.
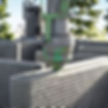




Revitri, LLC was incorporated in August 2023. This was done to facilitate the filing to the US Patent office submitted August 21, 2023 – Application #: 18/453,167. The patent submission is an accumulation of several years of development working through the cycles of engineering, chemistry, and tests to develop the high performing process.
Structural composites have been around for millennia. Ancient societies used rocks and sand to increase strength, improve weatherability, and enhance longevity of building materials. More recently, sand fillers have been converted into glass powder, fibers, or beads to further enhance composite materials. The use of glass and other mineral fillers like talc and calcium carbonate in composite systems such as thermoplastics, two-part resins, or concrete has allowed humans to build, form, mold, and create significantly stronger items than ever thought possible. While these have led to better parts and structures, the capabilities of the existing fillers and formulations have been exhaustively researched and the rate of high-impact innovation has slowed.
There are two novel manufacturing processes Revitri has developed. The first is the glass foamed bead. The second was discovered while developing the raw material source, recycled glass. A visit to a local recycler exposed us to the supply chain and abundance of their lowest grade of mixed cullet (glass). This grade currently has a limited market use and the over flow goes to the landfill! In the U.S., many states curb side recycling is a mixed together (paper, glass and plastic) and has to be separated at the recycling facility. The clear glass is separated and goes back to bottle manufactures. The middle grade sorted glass with contamination levels <.15% go to fiber glass insulation companies. The lowest grade has a contamination level of 1.5% to 2% has limited third party uses. Revitri has worked out a process to clean and crush this glass to obtain a high level of glass powder purity needed for the glass bead process. Developing this process insures a low cost raw material for Revitri while keeping the glass cullet from going to the landfill. Another win for the environment.
ABOUT
About Revitri
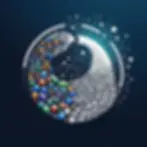
Below are images of beads from the lab and in test applications
From Our Laboratory
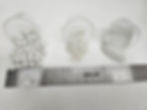



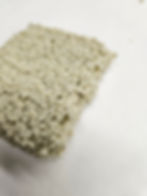
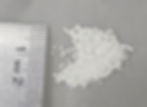

